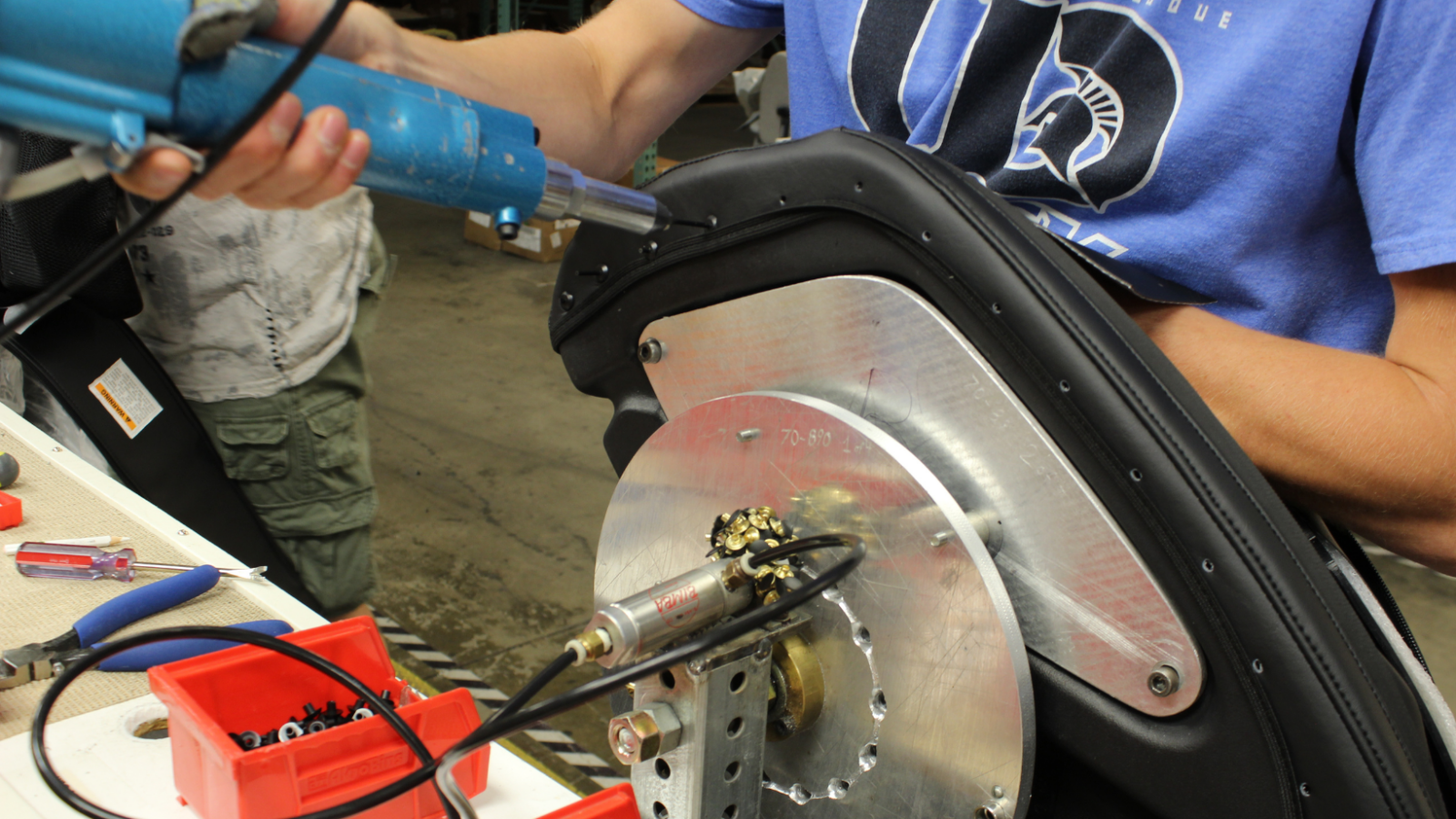
Polo Latest
Innovating the Future: Exploring Polo’s Manufacturing Capabilities
This pulls excerpts from our podcast, Inspiring Innovation: Leaders in Manufacturing featuring Carla DeShaw. To watch our podcast episode, please visit Inspiring Innovation Episode 10 – Carla DeShaw (youtube.com) or subscribe to our channel on your favorite podcast platform.
At Polo Custom Products, we are committed to delivering innovative high-quality products. To that end, we are always pushing boundaries and redefining what is possible in manufacturing. With experts on staff in sewing, sealing, and thermoforming, as well as product development, design, and more, we can ensure your needs are met, no matter how complex the project. Determining what manufacturing capability is needed for your project is an important step in the development process.
RF Sealing
RF Sealing is used to create airtight or watertight seals, which is crucial for many medical products and other products. RF Sealing or RF Welding uses high frequency radio waves, along with pressure and cooling to create the desired shape with watertight seals. The process fuses the layers together, taking two layers and bonding them to create one, which creates a stronger, thicker, heavier material. It is a great process for drainage bags, laparoscopic surgery bags, and more.
Utilizing the correct material for RF Sealing is necessary to create the perfect seal. At Polo Custom Products, thermoplastics or film layers such as PVCs or urethanes are the preferred materials for this process. It is best to steer clear of materials like polyethylenes, polypropylenes, mylars, Tyvek, and nonwovens because they aren’t good for RF Sealing.
Other Sealing Techniques: Hot Air Welders, Impulse Sealing, and Ultrasonic Sealing
Polo Custom Products has the capability to use other sealing processes depending on the needs of your project.
Hot air welders are easier to use because they don’t require the detailed tooling that RF Sealing does. This process is ideal for larger products such as large bags or duffle bags, as it provides flexibility in maneuvering large materials with curves and edges. It is the recommended process for complex or difficult areas to get in for sealing because you can seal more 3D with hot air welding. Thicker, heavier materials are recommended for this process.
Impulse welding, on the other hand, is quick, energy-efficient, and suitable for smaller products. The process bonds the material instantly and it’s done, which uses very little energy. You have the option to use a vast array of materials for this process, such as polypropylene, polyethylene, foils, mylars, and even Tyvek and nonwoven. However, this process requires detailed tooling that can be more expensive and have a longer lead time.
Ultrasonic sealing stands out as a precision-focused method, narrowing down to smaller sealed areas. With ultrasonic sealing, you’re able to seal straps, hooks, or loops together, but it’s on a smaller scale. Normally if we do a product with ultrasonic, it’s generally within 10 inches or less. Ultrasonic is intended for flat surfaces, so it’s not effective if you’re trying to seal corners or joints. It requires specialized machines and specialized tooling that can have lengthy lead times.
Industrial Sewing: Balancing Strength and Flexibility
When it comes to sewing lightweight materials, there are many factors to consider. One of the first considerations is the end use of the product and how the seams will be finished. Sometimes binding or reinforced stitching is necessary to ensure a high-quality product. Other things like material thickness, material stretch, and sewing machine type are important factors in sewing production. The choice between standard and walking feet, along with needle and thread selection, also plays a crucial role in achieving strength and flexibility in seams.
At Polo Custom Products, we are committed to solving complex problems for our customers. There can be unique challenges to sewing when it comes to meeting quality and standards. Our team recently had to design a stitch pattern on a strap that could hold 10,000 lbs. Through a collaborative effort, our team was able to develop a precise stitch pattern using the right thread to meet the stringent requirements.
Thermoforming
Thermoforming is a process essential for creating molds. With thermoforming, a material is heated to its softening point and then stretched, molded, and manipulated into the desired shape. This process requires a careful selection of material based on the intended application. Factors like ruggedness, wipeability, material stretch, and foam density, as well as considerations like what product may be going into the mold, are important in material selection for thermoforming.
Quality Control
Quality control is integrated into every step of our manufacturing process, from the beginning stages of product development through production and packaging. If a customer has specific quality requirements, those requirements are built into the processes required for their project. This helps us create the testing parameters necessary to ensure that the quality is consistent throughout the entire process.
At Polo Custom Products, we offer comprehensive, cutting-edge manufacturing capabilities. We are always working towards continuous improvement and adapting processes as needed when customers bring us new and exciting challenges. Our commitment to precision, innovation, and quality is evident in all of our processes. We remain dedicated to staying at the forefront of the industry, delivering high-quality products that meet and exceed customer expectations.
Please contact us with any questions or to request a quote!